Pictured Above: PUMP IT UP. A central tire inflation system can make quick work of changing a tire’s air pressure, whether that be decompressing down to 7 psi for the field (left) or pumping up to 20 psi for the road (right).
With the adoption of Increased Flexion (IF) and Very High Flexion (VF) radial tires becoming more widespread, farmers are now able to set up equipment to carry greater loads at lower inflation pressures than in the past.
This is good news. With equipment getting larger and heavier, it means no-tillers have a better chance of combating yield-robbing compaction by managing tire pressure.
Changing air pressure in a tire the conventional way might be too time-consuming or inconvenient and oftentimes just doesn’t get done in the rush to complete field work. But central tire inflation systems (CTIS) may be an innovation that will solve these problems.
Is a CTIS Right for You?
By Bradley Harris, Firestone Ag, Manager of Global Agricultural Field Engineering
(Editor’s Note: This excerpt originally appeared as part of a Q&A on James Tuschner’s AG Tire Talk. For the complete post, check out www.agtiretalk.com. See below for more on James Tuschner.)
In North America, not all tractors on a farm will need to be equipped with a CTIS system, and some farms will not need these systems at all.
A CTIS makes sense for tractors when the axle weight changes between road transportation and field operation. The most common scenario in North America would be the planter tractor with a two-point mounted, front-fold planter. During road transport, the planter wings fold forward and the planter weight is carried on the rear axle of the tractor and only 4 tires on the planter.
Weighing a 235 horsepower mechanical front-wheel drive (MFWD) tractor with a 16/32 row front-fold planter, the rear axle weight of the tractor is around 27,000 pounds during road transport. When the planter is unfolded in the field, the weight of the planter is now taken off the rear of the tractor and is being carried primarily by the 8 tires on the planter. Now the rear axle weight of the tractor is 16,500 pounds.
With dual 480/80R50 tires on the rear of the tractor, the farmer would need to set the inflation pressure to 23 psi to carry the 27,000 pounds for road transport. When the tractor is the field, 23 psi is an overinflated condition to carry the 16,500 pounds — 12 psi is sufficient.
Having the higher inflation pressure will not damage the tire, but it does reduce the tire’s footprint, which reduces traction in the field and increases fuel consumption.
The CTIS system doesn’t make financial sense on tractors where the axle weight doesn’t change between road transport and field use, like tractors pulling drawbar tillage and planting equipment that transfers little to no tongue weight to the tractor.
Using as example the same 235 horsepower tractor pulling a field cultivator or disc, the rear axle weight of the tractor remains consistent at 16,500 pounds and the inflation pressure required is 12 psi all the time. In this case, the farmer would not benefit from a system that changes pressures between road and field.
At the Touch of a Button
According to Ken Brodbeck, vice president of technology at Precision Tire Inflation, automatic tire inflation systems are perfect for any no-tiller who wants the increased footprint in the field that machines on tracks can provide but still want the higher speed, lighter weights, fuel economy and great ride on the road of a tire.
In effect, CTIS “changes the tire into a pneumatic track in the field and to a high-speed tire on the road while offering a lower upfront investment and maintenance costs compared to tracks,” he says.
“Central inflation systems allow you to run tires at the optimum traction and flotation that they’re developed for, both on and off the road. And by reducing the inflation pressure appropriately for field conditions, you’ll get a larger footprint in the field, which gives you more traction, more lugs in the footprint and less ground compaction.”
“For every half-inch the tire sinks into the soil, the equipment’s going to use an additional 10% of fuel…” – Ken Brodbeck, Precision Tire Inflation
Optimizing tire performance will also optimize equipment performance, lowering operating costs and increasing profits, he explains. Both public and private research has shown that a CTIS can provide a 4-6% increase in yield and a 10% fuel savings with a very modest investment, Brodbeck says.
“Farming margins are tight, and producers who can increase efficiency will survive these tough years and still put money in their pocket.”
Tires vs. Tracks
Overinflated tires will generally create more soil compaction than tracks, but the perception is that tracks never create compaction and that’s not true, Brodbeck says. “If you can get down to 8-12 psi (pounds per square inch) tire pressures per the tire manufacturer’s data book, the tires are going to compact the soil less than a tracked machine,” he says.
“In fact, we’ve had customers, who have planted corn and soybeans in the wheel track and saw no yield reduction in these rows. I wouldn’t have believed it if somebody had told me. Sometimes the yield is even a little better in the wheel tracks because it creates a nice consistent seedbed with very little variation in soil density.”
Optimal Pressure
To get the full life out of a tire without CTIS, tire pressures must be set for the worst-case condition, which is usually the road transport conditions where speeds are around 35 mph. But then the tire pressure that’s used for the road will also be used in the field.
“When you do that, you’re causing compaction in the field, and that’s what we don’t want, especially when you have wet or damp soils. And farmers understand that replacement tires are the second-highest maintenance costs for a tractor, exceeded only by something like a new engine or transmission,” Brodbeck says.
“So new tires, especially the high-technology, IF/VF ones, are a big investment. A good farmer wants to protect that investment and CTIS will do that.”
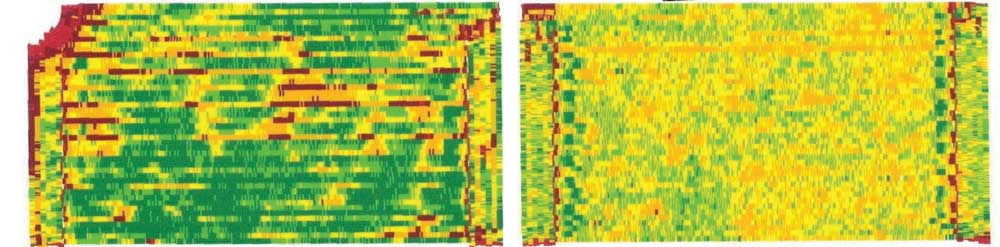
VISUAL EVIDENCE. Before (left) and after (right) imagery shows much more consistent field conditions after the installation of a central tire inflation system. In both cases, a 36-row John Deere DB90 planter was used, pulled behind a tractor with IF 480/80R50 and 380/80R38 front duals on the tractor. The red areas indicate significant soil compaction.
In addition, doing fieldwork on tires that are overinflated is simply inefficient.
“If you have those high pressures and you go to the field, for every half-inch that tire sinks into the soil, the equipment’s going to use an additional 10% of fuel,” he says. “Basically, think of the tractor as always trying to climb uphill out of that rut. That costs you efficiency.”
Tires can’t just be set at field pressure either. “Essentially, heat is a tire’s enemy,” Brodbeck continues. “And whenever you have higher highway speeds, a firm tire is a must. You have to have more air in that tire to keep it running cool, carry that heavy load on a hard surface and respond to steering inputs. You don’t want too soft and squishy of a tire.”
In the field, heat isn’t really an issue because of the slower speeds. Weight isn’t usually a problem either, at least with folding equipment, because as the equipment unfolds the weight transfers off the back axle of the tractor onto the implement, Brodbeck explains.
“In this scenario, the farmer should be inflating those tires to that higher pressure for the road, often 30-35 psi, which can cause compaction,” he says. “When they reach the field and unfold the planter, that weight goes off the back axle and goes into the soil and the individual planting units. If you have an inflation system, you then can dial that in and optimize that tractor’s footprint — high pressure for the road, low pressure for the field — and everything works a whole lot better.”
Many people might wonder what’s wrong with just setting the tire pressure somewhere between high pressure and low pressure, and not taking on the added expense of a CTIS.
“If you do that, you lose money on both ends,” says Brodbeck. “You’ll be running at a higher pressure in the field, causing excessive compaction, creating ruts and erosion and losing yield. And then when roading, since you haven’t inflated the tires to where they ought to be, the tires are literally scrubbing themselves off.”
Gaining Traction with Inflation Systems
Central tire inflation systems have been available for nearly 30 years on ag equipment in Europe, where tractors with single tires and three-point hitch equipment are the norm. The concept is relatively new to the U.S. However, inflation system technology is available in the U.S. as an economically feasible solution for compaction. Here are some systems to look for.
PTG Tire Inflation Systems
The German company PTG, acquired in 2017 by Michelin, has been developing and marketing agricultural tire inflation systems since the 1990s. Available in the U.S. from Precision Inflation, PTG offers a variety of high tech on-the-go inflation systems which quickly adjust tire pressures from the cab to tire industry recommended pressures for the road and field. PTG’s on-the-go systems are operated either through the tractor’s computer screen or a small digital control box.
PTG offers fully integrated systems with “behind the wheel” rotary unions and lines, or small exterior rotary unions and highly protected air lines.
All PTG systems are extremely durable, requiring no maintenance on the seals for 10,000 hours of operation. Pneumatically controlled check valves only pressurize lines when changing tire pressures. Equipment equalizes pressures across the axle within ½ psi. Once the system reaches the proper pressure, the check valve shuts off the air to the tire, so the air in the line goes to zero. No pressure on the seals or in the line, means no leaking.
For ag equipment that does not have an on-board air compressor, PTG also offers a variety of hydraulic-powered compressors including screw, vane and piston compressors in sizes from 20 to 140 CFM (cubic feet per minute) to allow fast inflation times for every need on tractors, sprayers, planters, manure haulers and more.
For more information, visit www.PrecisionInflation.com or www.PTG.info.
Zen@Terra
New from Michelin, Zen@Terra combines Michelin EvoBib or AxioBib tires, central tire inflation systems from PTG and in-cab dashboard control systems.
Up to 30 different tire inflation pressures can be stored for field and road operations. No matter which implement is used, the driver is able to choose the optimum tire inflation pressure with just a few clicks on the tractor’s terminal.
The different optimum pressures is determined through the “Agro-Pressure” app, which allows the user to input machine and tire data, including the real machine weights. After that, the calculated pressures are validated by Michelin and get uploaded via Bluetooth on the Zen@Terra Control unit.
Zen@Terra requires an ISOBUS-ready tractor terminal and ISOBUS-controlled PTG dual-line tire inflation system.
For more information, visit www.PTG.info/zen%40terra-eng.html.
Trelleborg CTIS+ Inside
Trelleborg’s CTIS+ Inside, jointly developed by Dana, is a full OEM-integrated central pressure control system that allows the tractor driver to inflate or deflate the tire pressure directly from the tractor cabin, according to the recommended pressure calculated by the Trelleborg Load Calculator (TLC) software.
During the inflation operation, the TLC algorithm instructs Dana’s Mechatronic Control Unit (MCU), which independently controls the distribution of air pressure for each wheel, through the Trelleborg manifolds installed on each inner rim. The Trelleborg manifold prevents air leakage between the stator and the rotary elements due to its design, which includes the Trelleborg in-house developed rotary seal.
Finally, the air reaches the tire chamber through an advanced wheel valve, which prevents the risk of leakages during operations. During the deflation, the TLC software and the MCU instruct the wheel valve to release tire pressure according to recommended values.
For more information, visit www.Trelleborg.com.
Fendt VarioGrip
Fendt VarioGrip is a tire pressure regulation system that adapts tire pressures from 0.6-2.5 bar (8.82-36.75 psi) quickly — even while driving. This is accomplished via the integral rotary union, which is designed to last the lifetime of the tractor. Air is supplied via a water-cooled double-compressor as well as the vehicle’s own valve equipment.
With VarioGrip, tire pressure can be adjusted in a matter of minutes using the VarioTerminal. With the VarioGrip tires inflated to 12 psi instead of the usual 26 psi, fuel consumption during field work can be reduced by 8% per acre.
For more information, visit www.Fendt.com.
Post a comment
Report Abusive Comment